Continuous Fluid Bed Drying System
Division for this product Plant Engineering and Machinery Division
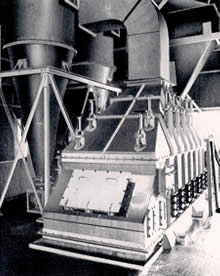
Summary
By feeding hot air in the material layer at rest from the bottom of gas straightening vane such as a perforated plate, when the material layer reaches a certain flow velocity (i.e., minimum air velocity for fluidization), it makes a minimal expansion from rest, enabling particles to start moving and leading to minimum fluidization. When the flow velocity accelerates a bit, particle groups gradually come to make active movements gradually. In that case, the hot air pressure loss due to the material layer comes to be in proportion to the weight of material particles on the unit area of the straightening vane. With further accelerating the flow velocity, the particle groups make vigorous movements to mix with gas in all directions, resulting in a state of suspension. The material layer expands to 1.2 to 1.6 times in height what it was at rest. Furthermore, it behaves as it is liquid and shows an appearance as it is boiling. This state is what is termed "Fluid Bed" and in stable state. Such fluid bed can be formed within a certain range of flow velocity determined with the particle size, specific gravity, and others of the material. Throughout the fluid bed step, the hot air pressure loss due to the material layer comes to be in proportion to the weight of material particles on the unit area of the straightening vane and remains constant.
Features
- Uniform temperature in fluid bed and exceedingly easy adjustments
In the fluid bed, the hot air and the material vigorously mix each other to prompt heat transfer. Therefore, you are able to maintain the temperature in the bed uniformly and make infinite adjustments of the temperature, minimizing the decline in the quality and non-uniform drying. - Large drying capacity
The large contact area of the material and the hot air and the rapid heat transfer provide large heat capacity coefficient ha (kcal/hro℃om2-fluid bed at rest), which sometimes reach ha=100,000 to 200,000 in the case of surface evaporation drying even though it is normally ha=2,000 to 6,000. - Drying up to extremely low moisture content
The residence time can be adjusted in the range from several ten seconds to several hours, making this system ideal for gradually drying up to extremely low moisture content. - Simple system structure providing stable operation
This system has almost no moving parts, allowing a simple structure and assuring low construction and repairing costs. The fluid bed can be formed with stability, enabling you to operate the system with ease.
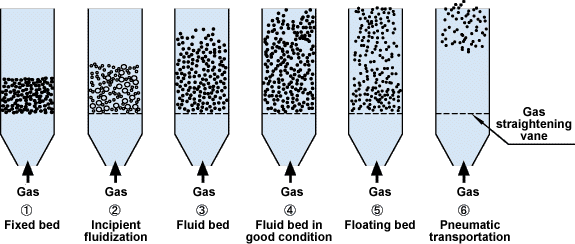
Construction
- You are assured of processing materials of hard fluidization property.
- You are assured of continuous separation and discharging of bulky particles.
- You are assured of getting right dry products.
With the continuous fluid bed, some distribution appears in the particle residence time, resulting in distribution in the moisture content of dry products to some extent. It is known that the moisture distribution becomes narrower with increasing the number of stages or chambers of the fluid bed. Therefore, by using multiple-stage or multiple-chamber fluid bed, you are able to minimize the distribution in the substantially harmless range.
![]() |
![]() |
|
Fig.-2 Horizontal multiple-chamber continuous fluid bed drying system (complete with an agitator) | Fig.-3 Coarse particle underflow discharge mechanism |
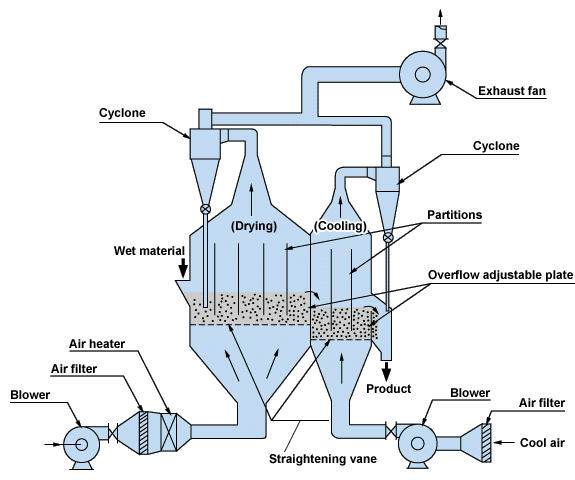
Fig.-4 Horizontal multiple-chamber continuous fluid bed drying and cooling system
Division for this page Plant Engineering and Machinery Division