Direct Heating Type / Indirect Heating type Rotary Dryer
Division for this product Plant Engineering and Machinery Division
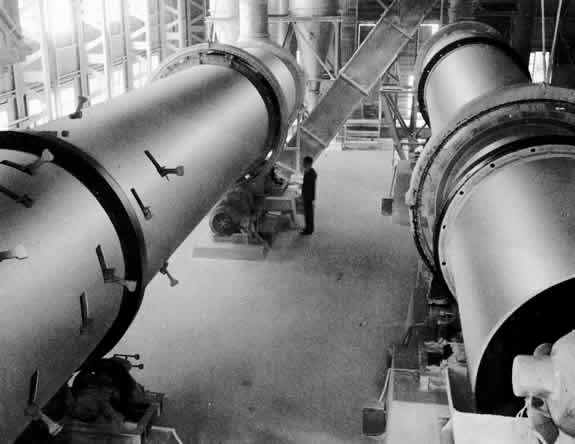
Summary
- Direct heating type rotary dryer
This is a direct heating type of dryer that brings materials into direct contact with hot air to dry them by lifting them up inside the rotary shell. - Indirect heating type rotary dryer
This is an indirect heating type of rotary dryer that brings materials into indirect contact with heating medium to provide heat exchanging.
The indirect heating type of rotary dryer is classified into external heating rotary dryer and steam tube dryer, which are applied for the following conditions.
- If you use materials that are easily affected by contact with combustion gas.
- If you need to minimize the amount of exhaust gas from the dryer.
- If you use materials that are apt to produce dust.
- If you use materials that are easily affected by oxidation.
- If you need to recover volatile component.
![]() |
![]() |
(Steam tube dryer) | (External heating rotary dryer) |
Construction
The main unit of the rotary dryer is an inclined shell supported by four rollers. Materials, which are fed through one end of the shell, move inside the shell along the inclination of the shell and through the rotary movement and are discharged from the other end. Materials, while moving inside the shell, are lifted up by a lifter incorporated in the shell. Then, the materials fall evenly in the shell space and exchange heat with the hot air flowing through the space to dry. Depending on the method of providing hot air for the materials, this dryer is classified into two types, that is, concurrent flow drying type by which the hot air and materials flow in the same direction and countercurrent flow drying type by which they flow in the opposite direction.
Lifter
The lifter is the most critical part having an influence on the performance of the dryer, which provides uniform dispersion of materials in the shell space. Any of the constructions shown below is used according to the physical properties of materials. Furthermore, spiral lifters designed with consideration of forced feeding of materials are used for the material feeding end.
(The above figure shows the constructions of respective lifters.)
Adjustment of residence time
By providing dams according to the applications, the materials residence time can be adjusted.
Prevention of adhesion and accumulation
In order to handle materials of high adhesive property, chains are provided in the shell or a hammering unit is provided externally on the shell, thus preventing material adhesion and accumulation.
Concurrent flow and countercurrent flow
Concurrent flow drying type
With the concurrent flow drying type, the materials move and the hot air flows in the same direction. Therefore, the hot air of the highest applicable temperature comes in contact with materials of the lowest applicable temperature at the end of the material inlet of the rotary shell. Normally, the concurrent flow drying type is used for the following conditions.
Countercurrent flow drying type
With the countercurrent flow drying type, the relation of flow direction and temperature between the hot air and the materials becomes reverse equivalent of the concurrent flow drying type. Therefore, this type is used especially in the case that low-moisture products are required, taking advantage of its characteristic that the hot air of the highest applicable temperature comes in contact with materials of the lowest moisture at the end of the material outlet.
Use
Concurrent flow drying type
|
|
|
Countercurrent flow drying type
|
|
|
Indirect heating type rotary dryer
|
|
|
Division for this page Plant Engineering and Machinery Division